Equipments
Gears
Introduction
Gear drives and speed reducers are widely used where changes in speed, torque, axis direction or direction of rotation are required between a primary motor and the driven machine.
In many power transmission applications, the primary engine operates at a relatively high speed. The driven equipment, however, generally requires much lower axle speed and high torque. The gear drive not only reduces the shaft speed for the required rotation, but it also converts the relatively low torque output of the primary motor to the high torque required to drive the device at low speed.
Many studies have been done in recent years to better understand the gear lubrication requirements. The ideal situation would be a theoretical solution that can predict the ideal lubricant for a specific set of gears and operating conditions based on easily measured system parameters. So far, gear lubrication has not been reduced to this pure science. Consequently, experience is still one of the most valuable tools for the proper selection of lubricants.
Lubrication provides the vital function of separating the contact surfaces of the gear teeth by a film that reduces friction, improves efficiency and increases service life. In addition, lubrication can also provide cooling and washing of gear tooth surfaces, corrosion protection and chemical modification of the surface material. While proper lubrication is a necessity for the successful operation of a gear set, it is not a cure for improper design, manufacture or operation.
TYPES OF GEARS
There are several types of gear configurations. Each type of gear has different design advantages and some have special lubrication requirements.
Common types of gears used in industrial transmissions include spur gear, double helical, helical, bevel, spiral bevel, hypoid, zerol, worm and internal gears (Fig. 1.1).
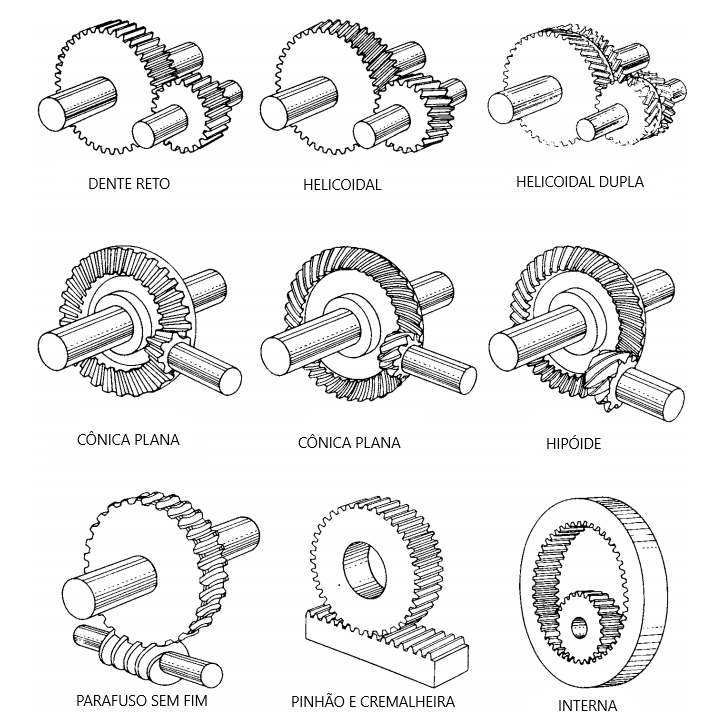
Figure 1. Types of gears. Source: CRC Handbook of Lubricant and Tribology.
This type of gear has the purpose of making variations in the force and speed of rotation of axles, by changing the size of the gear radius. It has straight teeth, which give the gear its name, and are usually installed on parallel shafts, connecting the teeth of one gear with the other.
This is one of the types of gears that can be easily found on the market and has a low cost compared to other models due to its simplicity in production, in addition to being compact, easy to install and highly reliable, however there is the disadvantage of producing noise in its functioning. This gear is commonly used to transmit large amounts of energy, and it does this extremely efficiently. It has a small percentage of dissipation and, thus, optimizes the process in which it is inserted.
They are commonly used in moderate speed drives, such as marine auxiliary equipment, lifting equipment, mill drive and oven drive. The simplicity of manufacturing, the lack of end thrust and the general economy maintenance recommend the use of spurs whenever possible.
HelicalHelical gears are built with teeth that are not aligned and parallel to the axis. Instead, they are angled to define an angle between the axis and the tooth segment.
An advantage of this type of gear is the fact that the teeth engage little by little, instead of the whole face at the same time. This generates a smaller impact, which is strictly related to the amount of noise produced. Thus, helical gears have a quieter operation compared to spur gears, for example.
Helical gears are used in various industry segments, however, being common in the automobile industry, in gearboxes, in the steel industry, in the railway and food industry, always having a wide connection with high loads and speeds. It must also be taken into account that, if noise is the main design criterion, it is necessary to choose the helical gear.
Bevel spurThe biggest advantage of the bevel gear is that it can change the direction of a turn and its strength, being able to transmit the energy between axes with different angles between them. Despite this, this is one of the types of gears that require very high precision in assembly. This is because the shape of the teeth of this type of gear causes the impact of the movement to hit one tooth at a time and, therefore, it can become rough and wear out over time.
Another point to be raised is the fact that this is one of the types of gears that do not support high speeds and loads, precisely because the teeth are not parallel to the teeth of the other gear to which it is connected.
Bevel helicalThe bevel helical gear, like the cylindrical gear, has clear differences from the bevel spur. Its shape allows a very large use of the energy that is offered to the gear system. The teeth, being slanted and of greater length, increase efficiency and reduce noise.
It is important to note that, because it is helical, it can withstand high loads and high speeds and, because of that, it must be made of material that supports the impact that one gear will receive from the other, to ensure safety and durability.
It is one of the types of gears that are used in machines with systems that can handle larger loads and in transmissions that need, in addition to load support, high transmission speeds.
Hypoidshttps://youtu.be/O-JTo0_Detw--> Hypoids are inserted in the bevel gears, however they have some peculiarities that have advantages over the others. The main one is to have the axes of the gears decentralized, that is, the lines of the axes do not meet. This allows for a translation margin for the second gear shaft, which is compact and can be used in limited spaces.
Another advantage is that hypoids have long teeth, which increases tooth coverage. For this reason, hypoid gears are able to transmit more torque than simple helical gears in the same space.
However, the separation of the shafts causes additional sliding of the teeth and generates a greater amount of heat, requiring the use of special lubricating oils, which are of high viscosity and must be applied periodically.
Hypoids have some common applicability with the bevel helical, however it is used in cases of larger loads and if it needs to adapt to some particularity. The car's transmission system, for example, uses the hypoid because it is silent and, mainly, due to the decentralization property of the axles. In addition to cars, they are also used in tractors and trucks with higher weights.
Spiral bevel gearsSpiral bevel gears feature slanted, curved, and spiral teeth, as the name implies. It carries with it the main properties of the conics, which is a greater support in terms of very high loads, quiet operation and the optimization of power transmission in relation to non-conics, having a greater efficiency.
Therefore, its particularity consists in the ability to operate with greater numbers of revolutions per minute without major problems. This allows this type of gear to be used in activities that have the objective of reaching higher speeds, such as the automobile industry.
In addition, the bevel spiral gear is highly requested when there is a need to change the rotation of an axis, since the inclined and curved configuration of its teeth allows such an operation. Its teeth are fixed at a certain angle, which allows the distribution of pressure and smoothness in the interaction of the parts, characteristics that allow adaptation to numerous activities.
Worm gearThe worm gear has gained wide acceptance in industrial drives because of its many advantages of joint action of the teeth, layout, compactness and load capacity. Worm gear drives are quiet and vibration-free and produce a constant output speed. They are suitable for services where heavy shock loads are encountered. The various variable mounting arrangements possible with worm gears allow for the compactness of the design that would not have been possible otherwise. Since the action between the auger and the teeth of the sliding driven sprocket is predominantly sliding rather than rolling, higher heat generation and lower mechanical efficiency result in higher speed reduction rates. In general, they have greater load capacity and work more smoothly.
The application of this type of gear occurs through clutch systems, in watches, elevator systems and in various industrial equipment that require high precision of movement and / or need a high speed reduction during the process.
GEAR LUBRICATION
The gear teeth can operate in three lubrication conditions: limit, mixed film and hydrodynamic. Limit lubrication occurs when the gear sets start or stop. At this time, the chemical properties of the lubricant are most important to avoid contact between the surfaces of the gear teeth. If gear sets were operated under limit lubrication conditions for long periods of time, wear would be rapid and severe.
As the relative movement starts and increases, the gear changes to mixed lubrication. Here, the roughness of the tooth surface is close enough to influence the friction coefficient. Under this regime, wear would occur at a slower rate than with limit lubrication, but it could still be too fast for a reasonable gear set life.
The ideal lubrication is a complete film, where the surfaces of the gear teeth are completely separated by a film of elastohydrodynamic oil (EHD) with at least two to three times the thickness of the roughness of the composite surface. As the lubricant viscosity is the most important characteristic in full-film lubrication, proper selection of the lubricant type is important.
LUBRICANT SELECTION
For an appropriate selection of the type, class and method of application of the lubricant, it is necessary to evaluate the following factors:
- Gear type - spur, worm, hypoid, etc.
- Size - pitch diameter, total depth and face width as an indication of the surface area to be lubricated.
- Assembly of the enclosure - Type of box around the gears. It is necessary to consider whether this housing will keep oil and oil vapors splashed and keep dirt, water vapor and other contaminants out, and whether the bearings are lubricated by the same system.
- Velocity - gear set speed.
- Load characteristics - It considers whether the transmitted power is continuous, constant, cyclical; possible shock loads and if there is high vibration; how often the unit starts; etc.
- Temperature - Range in which the lubricant should run. This includes the lowest ambient temperature expected at startup and the highest operating temperature.
LUBRICANTS
Lubricating oils for use with closed gears and reducers can be high quality or synthetic mineral oils and within the recommended viscosity ranges.
They must have good foam removal properties, good oxidation resistance, low pour point to reach the lowest expected temperature. When the operating temperature varies over a wide range, an oil with a high viscosity index is desirable.
Every precaution must be taken to prevent foreign material from entering the gearbox. The sludge is caused by dust, dirt, moisture and chemical vapors. These are the biggest enemies of proper lubrication on the transmission units.
The most common lubricants used today are: inhibited oils, extreme pressure, compounds, for open gears and greases.
Inhibited LubricantsThey are mineral oils containing rust and oxidation (R&O) inhibitors and perhaps antifoam or anti-wear agents. Rust inhibitors protect ferrous surfaces from rust. Oxidation inhibitors delay the formation of acidic contaminants, carbonaceous material and increased viscosity. The inhibited oils are generally suitable for spur gears, helical and bevel that transmit light to moderate loads. This type of oil can be used efficiently to cool the gear mesh and wash the tooth surfaces with wear particles or debris. The lubricant can be easily conditioned with filters to keep them clean and heat exchangers to maintain the temperature.
Extreme Pressure Lubricants (EP)These are basically inhibited oils with the addition of extreme pressure additives. The EP agent controls wear in the limit lubrication phase: stop, start, shock loads, etc. There are two basic types of EP agents. The first is chemically active, like sulfurous phosphorus, which reacts with the material of the gear tooth surface under high temperature to form a thin film of easily cutable material. If high points of the corresponding surfaces come into contact, the material in contact will distort rather than fuse and cause scratches. The second type of EP agent is a solid suspension lubricant. Solid particles (such as graphite, molybdenum disulfide, borate, etc.) stay between the surfaces of the teeth and prevent metal-to-metal contact. EP oils are used for spur, helical and bevel gears, where loads are very heavy for non-EP mineral oils.
Compound LubricantsGenerally, they are basic oil with high viscosity, composed of fat or tallow as lubrication additives to reduce friction. These oils are mainly used in helical gear drives, where the high sliding action of the gear teeth requires a friction reducing agent to reduce heat and improve efficiency./p> Open Gear Lubricants
They are high viscosity lubricants for large, low speed and heavily loaded gear sets. These lubricants contain adhesion additives to adhere to the gear teeth and resist being thrown out or squeezed out of the mesh. Some of these compounds are so heavy that they require solvents to lower the viscosity enough to be applied. The solvents evaporate and leave the thick protective film on the gear. As this type of lubricant adheres to the gear teeth, constant application is not necessary.
GreasesGreases are liquid lubricants thickened with soaps to a gel-like consistency. The soap retains the liquid portion and releases it as needed, analogous to oil in a sponge. The liquid portion lubricates with the advantages and limitations of the base oil used for loading and operating temperature. The advantage is that the lubricant does not need to be added continuously. Grease can act as a seal to keep out dirt and moisture. The disadvantage is that, unlike the continuous oil flow, the grease does not remove heat or particles from the gear mesh until the new grease is introduced and the old grease is displaced.
The grease can be used in spur, helical, worm and chamfered gears. It is generally restricted to low speed or very small components with light load and intermittent service. Higher speeds will cause the grease to "channel" or be displaced by the gear teeth, preventing the lubricant from reaching the areas where it is needed. Selecting an appropriate consistency from the National Lubricating Grease Institute (NLGI) is very important. Useful operating temperatures are limited by base oil and soap. For multipurpose greases, the useful range is approximately –30 to 120 ° C.
In addition to petroleum-based lubricants, a wide variety of synthetic lubricants is available. The cost of synthetic lubricants is higher than petroleum-based products, but they have definite advantages for special applications. Since many synthetics have much higher viscosity indexes than petroleum-based lubricants, their viscosity does not change as much as the operating temperature increases or decreases. Synthetic lubricants can also be used where fire resistance is required. When considering the use of a synthetic lubricant, the lubrication and load capacity must be evaluated, as well as the compatibility with paints, plastics, seals and sealing materials.
Solid LubricantsAnother class of lubricating materials consists of solid lubricants, such as graphite, molybdenum disulfide, fluorocarbon polymers, etc. Some solid lubricants can be used for applications at very high temperatures 540°C or more, or used with a liquid vehicle that evaporates or decomposes, leaving the lubricating material behind. Solid lubricants can be used where access to relubrication is difficult or where leaking lubricant can contaminate surrounding components.
LUBRICANT'S VISCOSITY DEGREE
After selecting the type of lubricant to be used, the appropriate viscosity level must be determined. A lubricant with very high viscosity will cause excessive heat to be generated, with excessive losses of energy and efficiency. A lubricant with very low viscosity will cause rapid component wear, resulting in reduced service life. Therefore, the lubricant with the lowest viscosity and which will keep wear rates within acceptable limits is the most desirable.
In reduction units consisting of multiple gear sets, the lowest gear speed is generally the most critical, as speeds are slower and torque is higher, and the type of lubricant would be selected to meet the requirements of this set. If a multiple reduction unit employed helical gears for reduction, this would represent the most stringent lubricant criteria. In general, each component in complex systems should have any special lubrication requirements assessed. The final selection of the lubricant must be suitable for all components.
Increasing the ambient or operating temperature requires more viscous oils, as increasing the oil temperature decreases the operational viscosity and reduces the thickness of the oil film. More viscous oils may be required if the unit is subject to shock loads or high levels of vibration. Oils necessary for performance over a wide temperature range should be selected with high viscosity indexes to reduce the effects of temperature on oil viscosity.